Is there a Lean Six Sigma alternative? Absolutely. Your existing LSS program can be improved by using the Perigon Method. We are often asked to compare Lean Six Sigma with Perigon.
Designed originally for manufacturing improvement, Lean Six Sigma focuses on removing waste and defects using the Define, Measure, Analyze, Improve, and Control (DMAIC) methodology. Business Enterprise Mapping’s Perigon Method uniquely builds upon the LSS toolkit to analyze a larger scale of work definition and connectivity that delivers greater change and overall improvement. As complementary tools, LSS and Perigon together provide a powerful capability to address the most difficult organizational problems through engaging, structured and insightful analysis. Perigon adds a far more robust business process mapping tool that increases the effective application of LSS.
Here are a few ways Perigon enhances the use of Lean Six Sigma in organizations today.
Perigon as a Lean Six Sigma Alternative
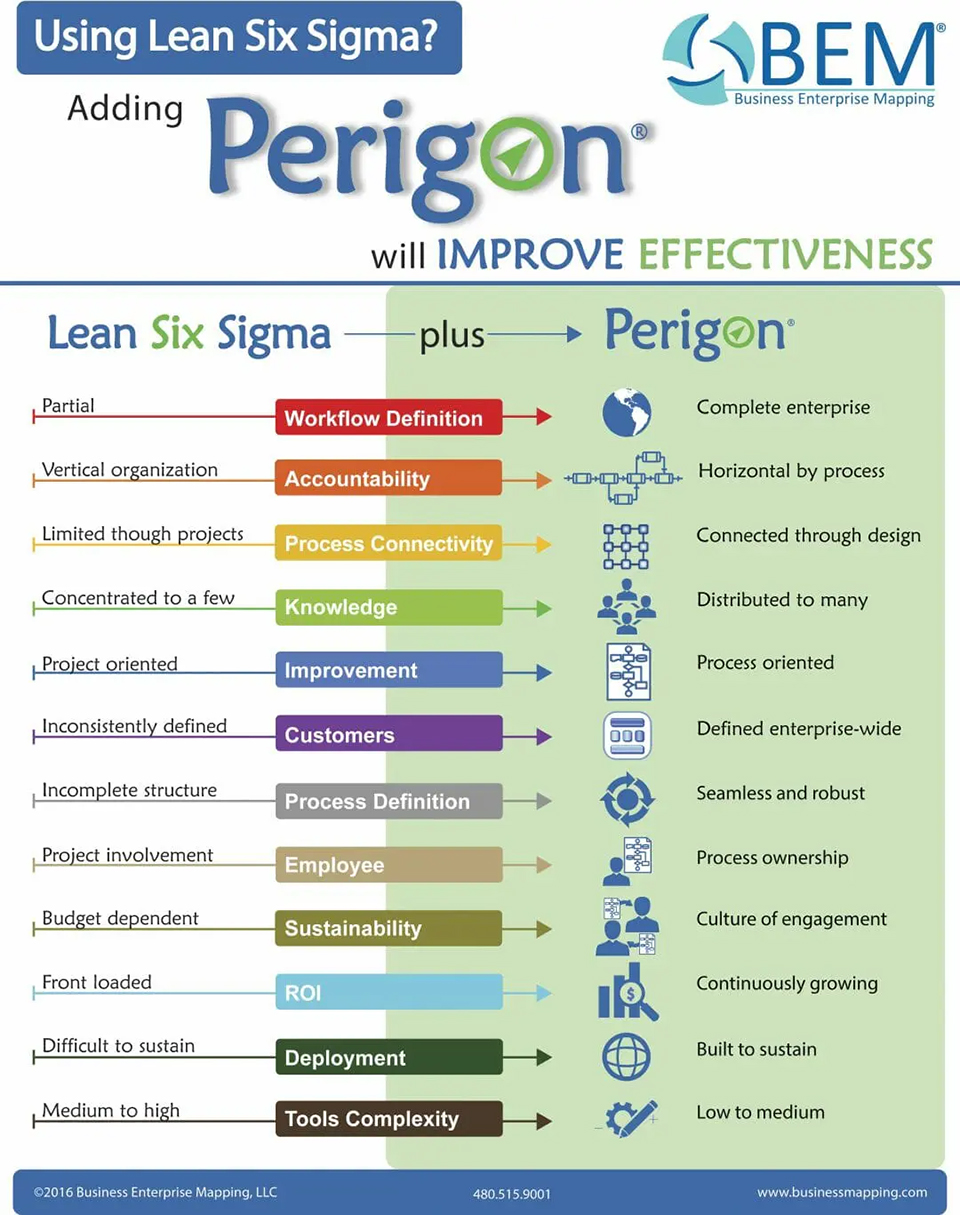
Process vs. Project-Based.
Lean Six Sigma efforts generally approach improvement goals through projects. The Perigon Method expands the LSS scope of workflow definition through business systems across an organization. This approach looks at the bigger picture in a way that forces organizations to rethink workflow, address communication silos, and proactively measure the most important cross-boundary indicators.
Accountability.
In traditional organizations, responsibilities are managed vertically with job responsibilities delegated from the top down. This often leads to disconnected department silos. Departments that should be working together may not even be aware they depend on one another for mutual success. Through the horizontal workflow definition of The Perigon Method, organization accountability is distributed through workflow-based outcomes.
Employee Engagement.
While Lean Six Sigma involves employees in working on defined projects, these projects are typically driven by LSS experts who fail to create long-term process ownership. LSS tools can be sophisticated and employee involvement is often limited to data collection and brainstorming efforts. The Perigon Method is dependent upon facilitating those who do the work to improve their work. The Perigon Method uses more available tools and is more driven by the knowledge and expertise offered by front lines employees to address the existing problems and opportunities that they know is preventing business improvement.
Customers.
Who are your customers? The answer may surprise you. While the customer value model is generally not standardized for Lean Six Sigma, The Perigon method builds significant and consistent Value Proposition and Customer Value Assessment Models. The Perigon Method defines customers as the person, process or organization – internal or external – using the product or service provided by the process to solve a problem or satisfy a want or need. It includes internal customers, external customers and even customers of customers.
Deployment.
Sustaining Lean Six Sigma improvement is often challenging for organizations. The Perigon Playbook is specifically designed for sustainable process ownership and improvement. Perigon engagement is viral in the organization and improvement efforts naturally grow as alignment and connectivity improve.
While Lean Six Sigma offers benefits to any business, The Perigon Method adds additional insight and capability to help you build and sustain changes within your organization.
Further Reading: THE PERIGON METHOD