In today's competitive business environment, the ability to understand and improve processes is crucial for efficiency, quality, and overall success. Yet, analyzing a process effectively requires more than just observing how work flows. A comprehensive process analysis systematically examines multiple dimensions — from how value is created to how efficiently resources are used.
Below, we walk through eight key dimensions of process analysis, offering a practical framework for evaluating and improving any business process.
1. Value Added: The Assessment of Waste
At the heart of process analysis is understanding value-added work. Value-added activities are those that directly contribute to meeting customer needs and expectations. Every step in a process should either create value, transform inputs into outputs, or be legally required.
Waste represents activities that consume time, resources, or effort without delivering value. These include overproduction, waiting time, transportation, over-processing, excess inventory, unnecessary motion, and defects.
To assess value added:
- Map out each step in the process.
- Categorize each step as value-adding, necessary but non-value-adding, or pure waste.
- Focus improvement efforts on eliminating or reducing waste wherever possible.
By maximizing value-added activities and minimizing waste, organizations can improve productivity, reduce costs, and enhance customer satisfaction.
2. Responsibility: The Assessment of Authority
A process is only as strong as the clarity of responsibility within it. Confusion over who is responsible for decisions, approvals, and task execution can lead to bottlenecks, rework, and inefficiency.
When analyzing a process, assess how authority and responsibility are assigned:
- Is there a clearly defined Process Owner?
- Are decision-making responsibilities aligned with the people closest to the work?
- Are there overlaps or gaps in accountability?
Tools such as a RACI chart (Responsible, Approval, Consulted, Informed) can be invaluable for clarifying roles and ensuring that responsibility is properly distributed across the process.
3. Information: The Assessment of Knowledge
Information is the fuel that drives process execution. Without the right information at the right time, processes slow down, errors increase, and quality suffers.
When assessing information flow:
- Identify what information is required at each step.
- Verify whether employees have access to accurate, up-to-date, and complete information.
- Evaluate how information is shared between departments, systems, and individuals.
A strong process ensures that knowledge is not hoarded, lost, or misunderstood. Clear communication protocols, accessible documentation, and effective training are critical to maintaining information quality throughout the workflow.
4. Records: The Assessment of Documentation
Good documentation underpins effective process management. It provides evidence of completed work, supports regulatory compliance, and preserves organizational memory.
During process analysis, examine:
- What records are created or maintained at each stage?
- Are these records necessary, accurate, and complete?
- Are they stored securely yet accessibly?
Records that are redundant, poorly maintained, or overly cumbersome can bog down a process. Streamlining recordkeeping requirements and transitioning from manual to digital records where possible can deliver significant efficiency gains.
5. Cycle Time: The Assessment of Synchronization
Cycle time measures the total time from the start of a process to its completion. Analyzing cycle time helps assess how well process activities are synchronized and whether work flows without unnecessary interruption.
To evaluate synchronization:
- Measure the average cycle time for key process instances.
- Identify bottlenecks, delays, and handoff inefficiencies.
- Compare actual cycle times to customer expectations and business goals.
A tightly synchronized process minimizes wait times, improves throughput, and enhances responsiveness to customer needs. Techniques like value stream mapping can visually highlight areas where synchronization is breaking down.
6. Resource Productivity: The Assessment of Asset Performance
Effective processes make good use of the organization’s people, equipment, technology, and facilities. Poor resource productivity often results in higher costs, lower output, and strained operations.
Key questions to ask:
- Are people’s skills matched to their assigned tasks?
- Are machines and systems operating near their capacity without excessive downtime?
- Is space being utilized effectively?
Measuring resource productivity involves calculating outputs relative to inputs, such as output per labor hour or equipment uptime rates. Improving asset performance often requires better scheduling, preventative maintenance, automation, or cross-training employees.
7. Process Efficiency: The Assessment of Execution Performance
Efficiency evaluates how well a process uses resources relative to the value it creates. Even if a process is synchronized and assets are performing well, excessive consumption of materials, energy, or effort can erode margins and competitiveness.
To assess process efficiency:
- Track the amount of raw materials, energy, and labor consumed relative to outputs.
- Benchmark against industry standards or best practices.
- Identify high-consumption steps that can be redesigned or optimized.
Lean techniques, Six Sigma tools, and kaizen events often target consumption performance to drive continuous process improvement and cost reduction.
8. Process Effectiveness: The Assessment of Solution Quality
Ultimately, a process must reliably deliver outputs that meet or exceed customer expectations. This is the domain of process effectiveness — how well the process achieves its intended purpose.
When analyzing effectiveness:
- Measure defect rates, rework levels, customer complaints, and warranty claims.
- Evaluate whether the process consistently meets its quality standards.
- Examine customer satisfaction and loyalty metrics related to process outcomes.
Improving process effectiveness often involves not only fixing operational defects but also understanding and addressing root causes at the system level.
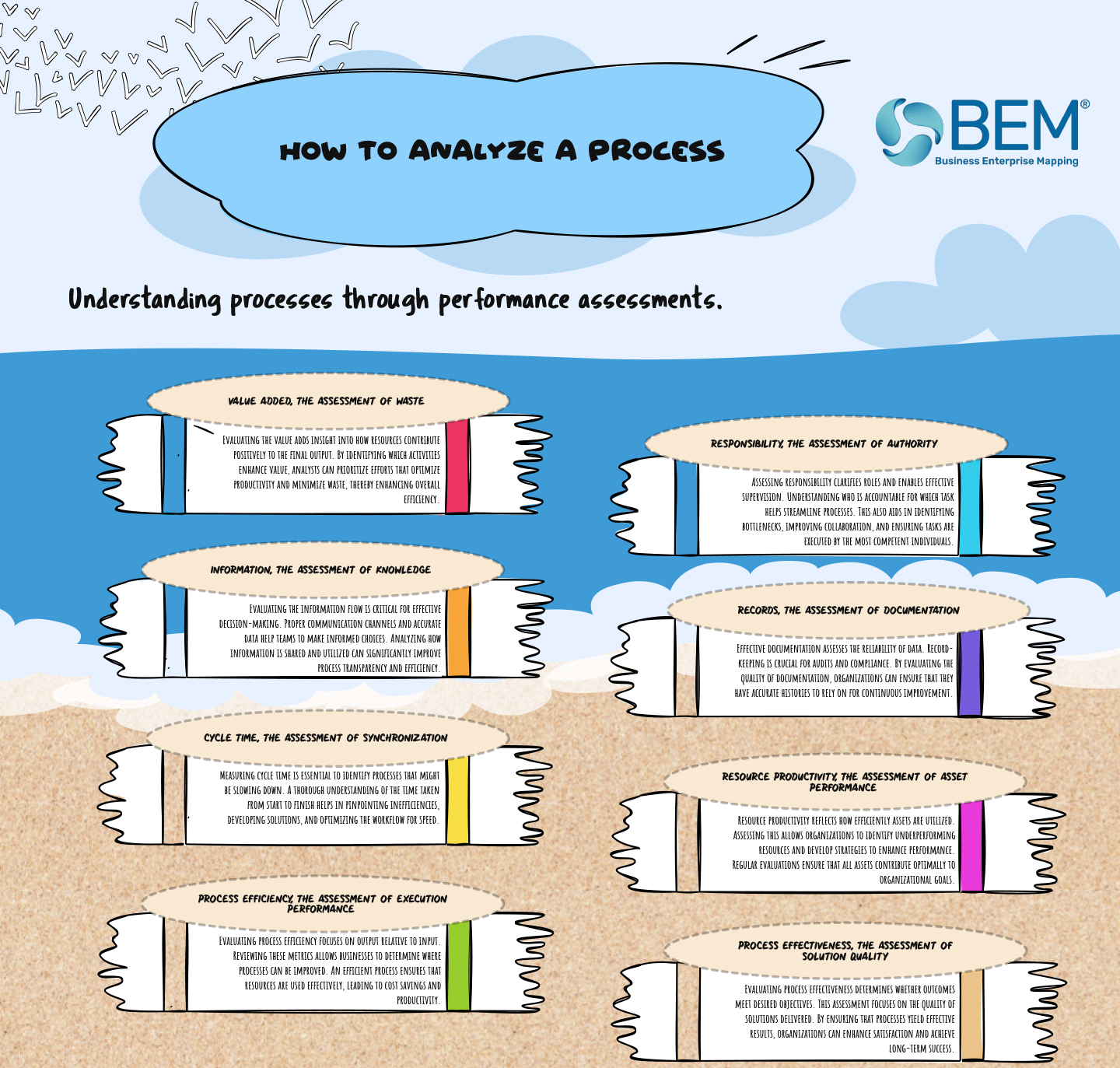
Conclusion: A Holistic Approach to Process Analysis
Effective process analysis looks at much more than just workflow. It demands a holistic examination across multiple dimensions: value added, responsibility, information flow, documentation, synchronization, resource utilization, consumption, and output quality.
By systematically evaluating each of these areas, organizations can:
- Eliminate waste
- Clarify roles and responsibilities
- Enhance information and documentation practices
- Synchronize workflows for faster cycle times
- Boost resource productivity
- Reduce unnecessary consumption
- Strengthen quality and customer satisfaction
Process analysis is both an art and a science. The art lies in asking the right questions and engaging the right people. The science lies in using metrics, models, and data-driven insights to guide improvements.
Businesses that regularly and rigorously analyze their processes position themselves for continuous improvement, operational excellence, and sustainable success.