At BEM, we have worked with over 300 clients over the past 25 years. During this time, we have encountered business processes in every type of industry and environment imaginable. Among the characteristics we study in a business process is the business process cost. This is an area where client employees frequently struggle, particularly when mapping a non-product producing or internal administrative process. The answer given by most Process Owners of an internal or administrative process is that there is no cost of that process. We know, of course, that there is a cost for every business process and it is in the organization’s best interest to know and manage that cost. What’s most interesting about this discussion is that the cost model does not vary by process type. What varies is the application of cost elements and cost drivers. With that in mind, shown below are the basic cost elements of any business process.
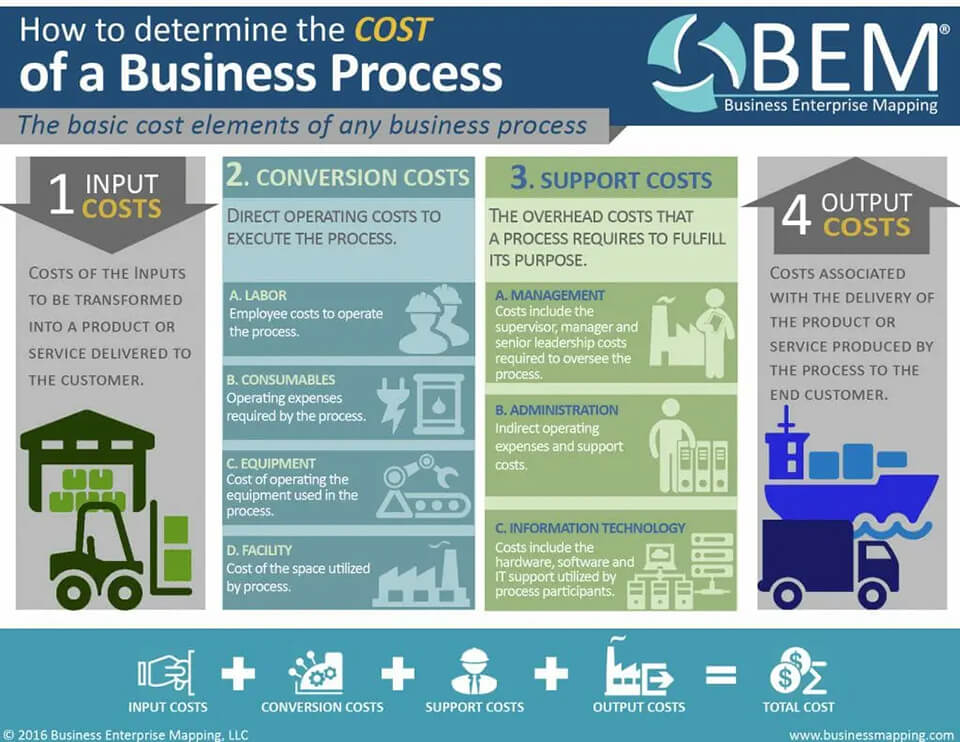
Business Process Cost
Input Costs are the costs of the inputs to be transformed by the process into a product or service that will be delivered to its customer. They are the bills of material that are input to the process for purposes of transformation. In a physical product, input costs are easy to identify, as they are usually the materials that will be changed by the process. When a process delivers an intellectual product or service, input costs are much more difficult to define. In this case, they may carry zero cost, which tends to confuse the Process Owner.
Conversion Costs are the execution costs of process transformation in order to convert inputs into outputs. Conversion costs are the direct operating costs of executing the process, which include the following categories,
- Labor is the cost of performing the connected tasks that together execute the process. It should include all of the costs of that conversion labor, Including wages, taxes and benefits.
- Consumables are the operating expenses required to perform the tasks that execute the process.
- Equipment is the cost of operating the equipment used to execute the process transformation. This includes the operating expense of the equipment itself, as well as the depreciation cost of the equipment.
- Facility is the cost of the space utilized by process users to execute the process. This is generally the square feet used by process participants and the associated cost per square foot of the facility in which they reside.
Support Costs are the overhead costs that a process carries to execute its purpose as connected to the larger business system. These are the indirect costs that organizations carry in support of business process execution. They include the following items.
- Management costs include the supervisor, manager and senior leadership costs required to oversee the process transformation. These employee costs should include all costs associated with the headcount including wages, taxes and benefits.
- Administration costs are the operating expenses and indirect costs of support necessary to execute the process. These include department expenses and support staff that do not directly impact the process but are part of the larger business system where the process resides.
- Information Technology is the cost of hardware and software utilized by process participants in the process transformation, as well as the IT system support costs for the process.
Output Costs are the costs associated with the delivery of the product or service produced by the process to the end customer of the process. These are commonly thought of is the distribution costs associated with moving a finished product from process to customer.
Every Business Process Has a Cost.
A process cost can be determined for any process using the basic formula outlined above. While the particular characteristics of the process will impact the cost drivers for that process, the categories of consideration do not change and all process costs are discoverable. Sometimes these costs are directly assigned to the process and other times they must be indirectly allocated. Either way, we advocate beginning with the best process cost information that is readily available and continuing to refine those costs by better understanding the cost drivers of the process.
Further Reading: THE PERIGON METHOD