We have been implementing process management and improvement for twenty-five years and we still find that many new clients do not have mature process management capabilities. Internal improvement efforts are often focused on solving immediate problems and fighting fires while missing the opportunity to build a core process foundation that delivers the capability to run the business better. Summarized below are ten characteristics of a process management system that we believe is necessary to successfully transform an organization from a traditional top-down management structure into a successful process management and improvement enterprise.
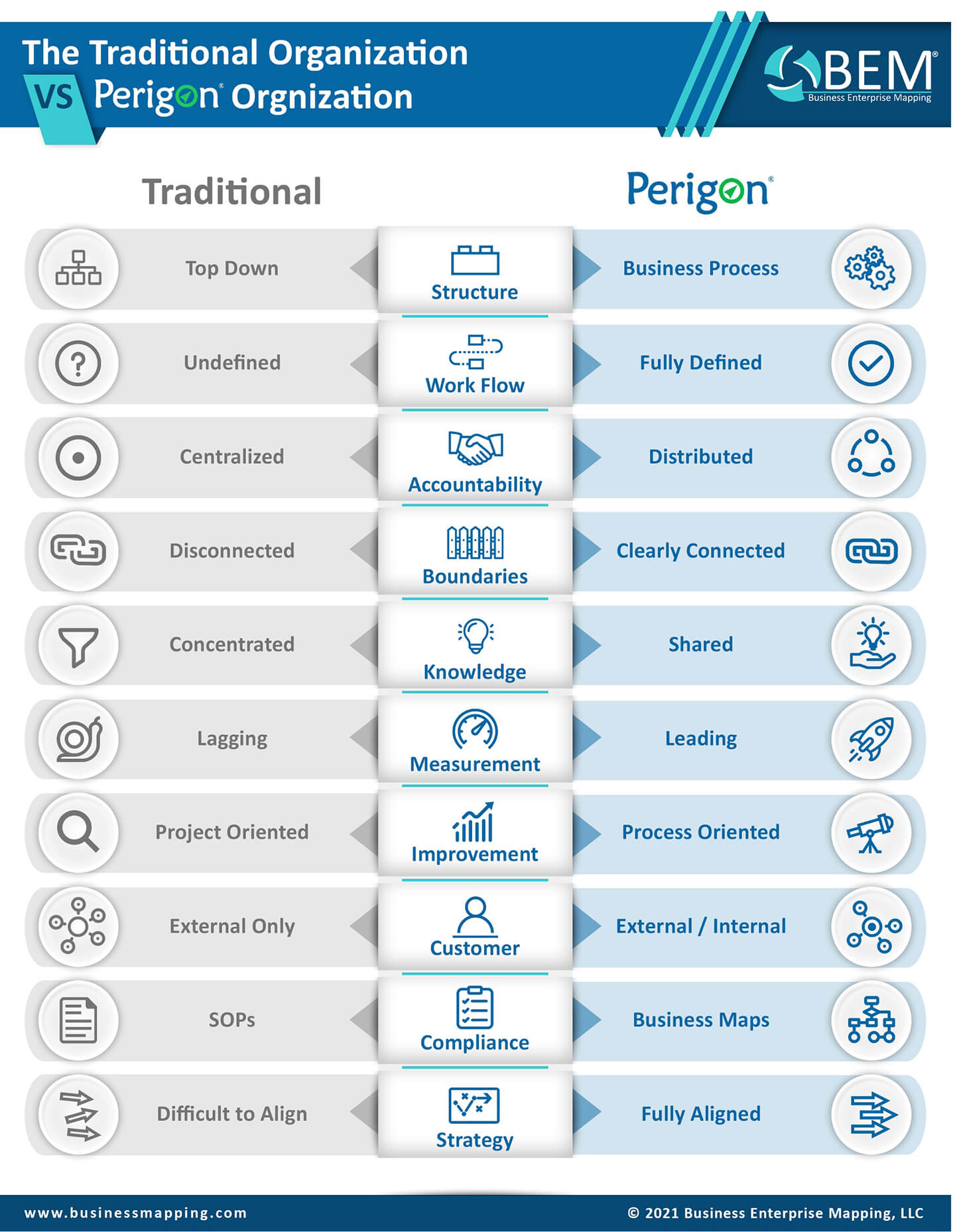
LET'S WORK TOGETHER
A Successful Process Management System
1. Purpose
Probably the most important success characteristic is that every process has a purpose. A worthy purpose requires that a customer exists with a need that is satisfied by the process, and an input is delivered by a process supplier that is then transformed into a product or service that the customer values. Every process should have a value proposition that serves a loyal customer and fulfills their important need. A process that does not have a worthy purpose should not exist.
2. Engagement
Employee engagement is essential for a successful process management system. A process that is defined by those who do the work will deliver the most accurate and meaningful process understanding that the organization can develop. The better the employee engagement, the more likely the process will be successfully defined, executed, improved and followed. Employee engagement should include those who operate the process, users of the process, subject matter experts who contribute meaning to the process, and process customers and suppliers.
3. Ownership
A process will not be well understood, improved and sustained without high-quality commitment and employee ownership. In implementing process base management and improvement, rethinking organization responsibilities and accountabilities around process ownership is an essential characteristic.
4. Definition
Good process definition may be the most difficult element of a successful process. Many of our clients have trouble defining a current state process, as many processes are executed informally and somewhat randomly. We also see many organizations define their processes at a level that is too high to capture a real understanding of the tasks, knowledge, decisions, and responsibilities that impact the workflow.
5. Connectivity
Defining process connectivity and creating boundary relationships is a necessary characteristic and one that we find is typically missing. Many organizations that we work with do not understand that customers directly receive a product or service that a process produces and delivers. Creating that connection can be difficult to understand. When we know who our customer is, we can create a partnership to improve our value proposition, which increases customer loyalty. Likewise, we have a similar opportunity on the supplier side of the process boundary. It’s the Process Owner’s responsibility to provide good process specifications to suppliers so that they can satisfy process needs.
6. Analysis
Process analysis can take many forms, but at the very least process analysis should include a value analysis, a handoffs analysis, a cycle time analysis, a process yield analysis and an assessment of customer value. There are many additional process analysis strategies that can be taken on to accomplish specific process improvement objectives.
7. Measurement
Nothing can be improved without measuring first. Most organizations measure what is easy, not what is important. Process measurement can take a variety of forms, including customer effectiveness, process efficiency, resource productivity, product and services quality, and process response time. It is important to measure what is important to improve.
8. Improvement
Every successful process must have an actively maintained process improvement plan. Continuous improvement requires a never-ending flow of new opportunities that need to be addressed to replace improvement actions that already have been implemented.
9. Monitoring
Once the process has been defined, analyzed, measured and released with an improvement plan, continuous monitoring needs to take place to ensure that the process is meeting expectations and getting better. This monitoring typically takes place on a weekly or monthly basis. Monitoring should include a review of the current performance of the process, the current status of improvement implementations, with a forward scan to near-term activities and changes to be made.
10. Sustainability
Sustainability may be the most important consideration to the long-term success of a process management system. Many process improvement projects begin with great momentum, do a good job getting process definitions in place, identify problems that need to be solved, implement measures and analytics to solve those problems, and then fall down during implementation. Sustainability requires all of the nine characteristics identified above, but most particularly engagement, ownership, and monitoring. An organization must make the commitment to continuing to strengthen business processes as a core strategy to improving enterprise performance.
We challenge you to look at the ten characteristics above and assess whether your organization is delivering a successful process management system and is operating to its full potential. In our experience, very few organizations manage processes well and strengthen them over time. As we have quoted often, over 70% of all problems and opportunities that we see originate from some process deficiency. Processes provide the engine that drives the enterprise, while strong processes are necessary to turn assets into profits.